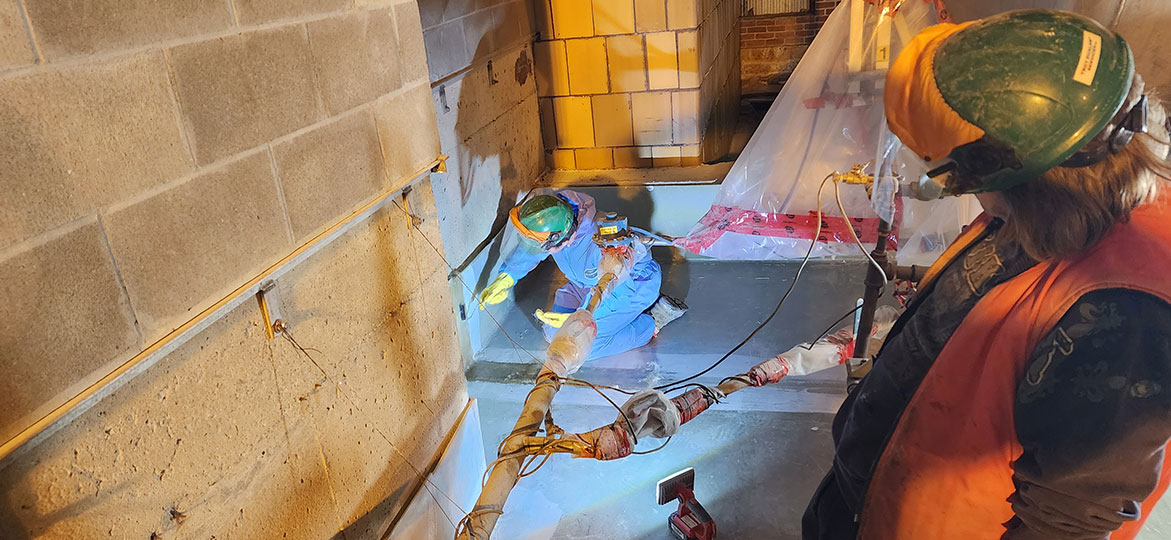
Description Of The Request
A retention basin situated on an upper floor of the plant has encountered major structural issues, resulting in significant failures. These failures have caused water or other substances to infiltrate the basin’s material, potentially leading to leaks or damage to surrounding equipment or infrastructure. This poses a serious risk to the plant’s operations and could result in costly repairs or downtime if not addressed promptly. The situation requires immediate attention to prevent further deterioration and ensure the safe containment of any liquids or substances held by the basin.
Outcome
The solution involves a multi-step approach to address the retention basin’s issues effectively. First, precise measurements will be taken on-site to assess the basin’s dimensions and the extent of the problem, ensuring that the replacement or repair fits the existing structure perfectly. Based on these measurements, a custom FRP (Fiberglass Reinforced Plastic) retention basin will be pre-fabricated in detachable parts, allowing for easier transportation and assembly. This custom fabrication ensures that the new basin is tailored specifically to the plant’s needs and can withstand future use without risk of failure. Once the components are ready, the team will transport them to the client’s site and carry out the installation, ensuring that the new basin is securely fitted, fully functional, and integrated into the plant’s system with minimal disruption to operations.
The Result of Project
Following the successful completion of the project, the retention basin issues were fully resolved. The custom FRP (Fiberglass Reinforced Plastic) basin was pre-fabricated according to the precise measurements taken on-site, ensuring a perfect fit. The installation process went smoothly, with the detachable parts being efficiently assembled at the client’s facility. The new retention basin is now fully functional, providing enhanced durability and leak prevention. This solution not only corrected the previous infiltration problems but also significantly improved the structural integrity of the basin, minimizing the risk of future failures. The client’s operations have returned to normal with no further disruptions, and the plant now benefits from a reliable, long-term solution to its containment needs.
OUR CLIENTS
PAST & CURRENT CLIENTS
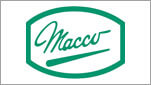
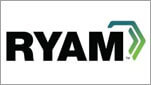
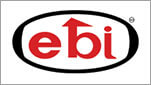
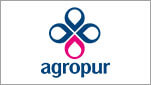
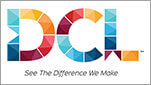
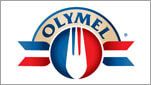
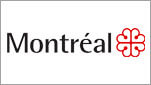
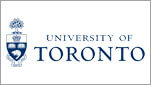
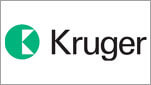
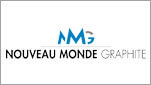
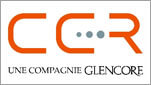
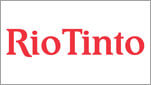
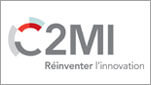
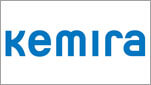
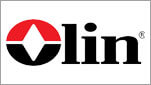
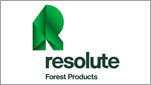
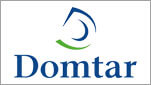
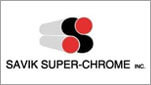
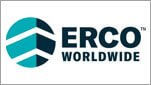
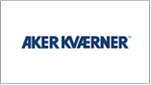
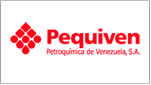
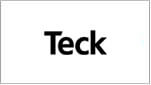

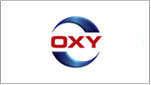
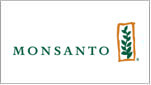
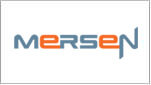
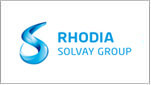
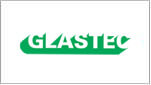
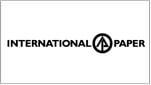
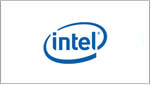
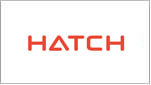
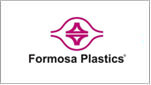
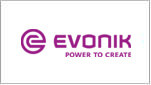
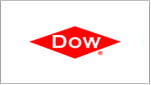
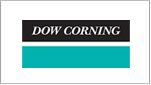
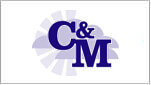
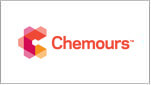
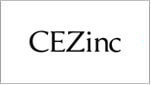
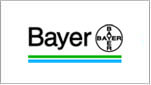

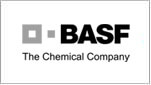
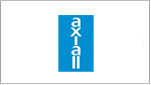
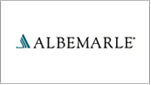
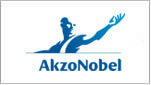
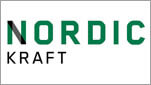